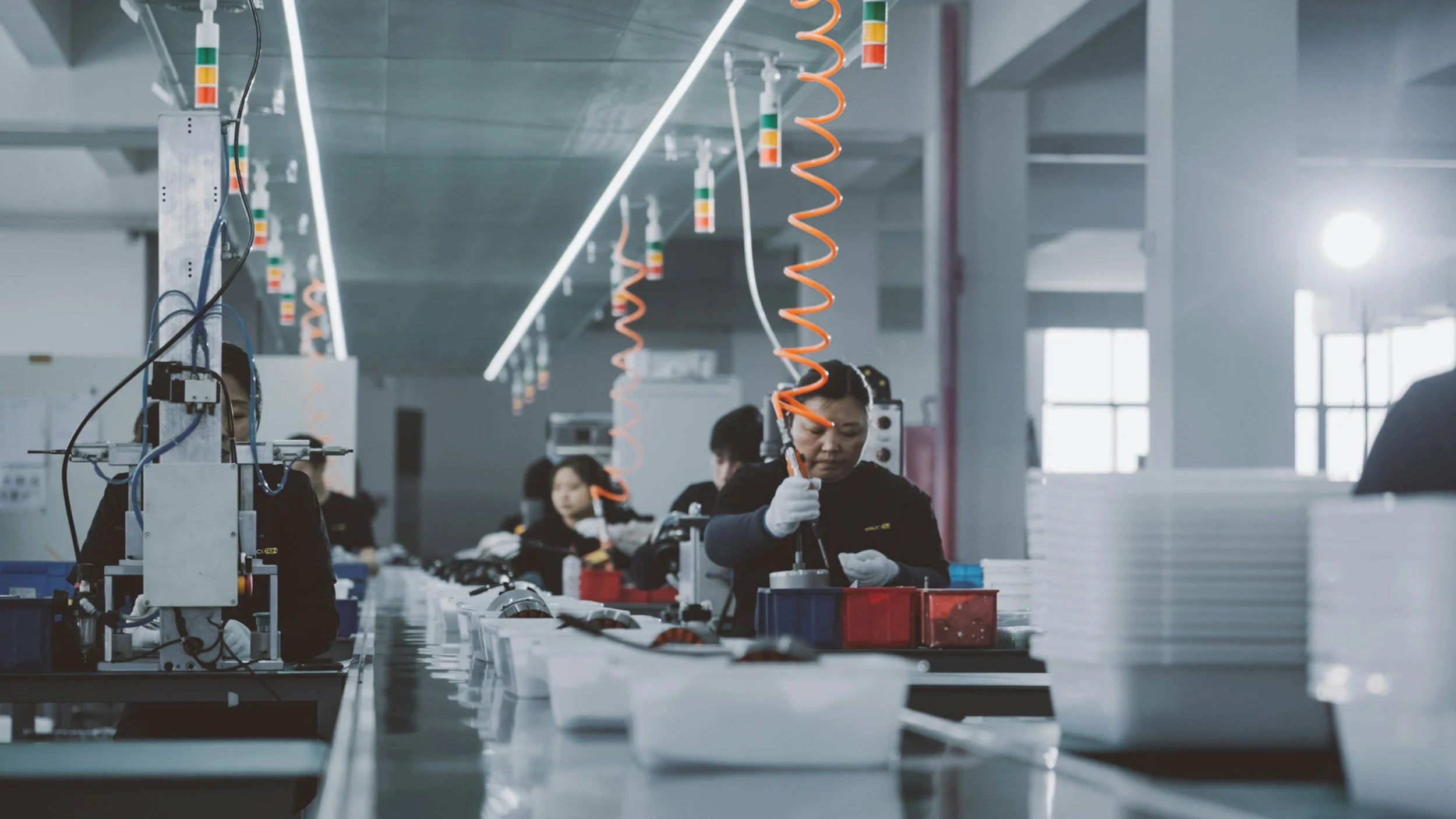
Project:
Paint Shop Management
General Motors
Overview & Objective
The General Motors Paint Shop had an existing legacy application written in an out-dated language — which led to disruptions during their workday and confusion with plant floor worker tasks, resulting in a slow down in production. My task was to re-skin the UI with a more intuitive interface as well as refine the user experience overall.
Discovery & Research
During the discovery phase we had the opportunity to visit the manufacturing plant in Arlington, Texas. While doing field research, my colleague and I received a tour on how the production line worked, showing how all the plant floor tasks integrated together. This process started all the way from putting pieces of the car together, to the car being ready to drive with safety checks in place before hand-off to car dealerships. Unfortunately, the paint shop was closed off due to strict safety issues in place. However, I did get to speak to a worker who used the plant floor application I was designing for along with one other designer. A few major pain points the plant floor worker explained was a slow performance with their application, and it being difficult to take their gloves off in order to complete or view a task. He also explained the importance of UI scalability from a desktop to a tablet device.
Being able to talk to the end user in their work environment of the product was extremely advantageous. This allowed me to better cater to his needs in the application, especially seeing the fast pace environment the user uses the application in. This allowed me to realize the application demands a quick and seamless UX for time sensitive transactions.
Business Context
The fast pace paint shop environment the worker is using the application in demands a quick and seamless UX for time sensitive transactions. This environment poses unique restrictions, for example — needing gloves while using the application on a tablet. Their current system lacked speed an intuitive features. This is immensely important because even a 5 minute slow down in a paint shop can result in a loss of $30,000 per minute, which amounts to $150,000 every 5 minutes. To put it in even more perspective, If a situation like this happened once a week, the company would lose $7.8M a year. This is why it is critical that time sensitivity is at the forefront in manufacturing environments.
Design Iteration Stage
After doing field research, I felt more confident in creating quick, iterative, high-fidelity designs based on customer feedback. Some of these we shared with the client are shown below.
Outcome & Impact
During the showcase of our final design, we were able to get a few users of the application to our office in Austin, TX, where we passed around a tablet with a working clickable prototype, with our designs implemented. Luckily, they thought it felt so real, for a moment, they forgot it was not a fully developed application yet. Along with being pleased with the design, they were also very pleased with a solution we presented to them with the idea of gloves that allowed for pressing on screens, with sensory circles on the fingertips. This was during a time where these types of gloves were not as easily accessible as they are today, so the client was extremely satisfied with that solution. This allowed them to complete tasks without having to take on and off their gloves repeatedly, in a face paced environment, which ultimately saved 50% of task completion time, and assumably saved a large quantity of money overall.
Prior to me and my co-worker starting this project and creating designs, the client was hesitant to hire developers and see the solution through, because although they already had an existing system that was slow, they still were able to get tasks done with some hiccups here and there. This led to hesitation, until we were able to show the value add.
After showing them the clickable prototype, and allowing them to click around at the functionalities, they realized this would save them time and money, and we ultimately proved this would be a wise investment to implement for their paint shop.
A team was eventually staffed to these designs, and later we found out it it resulted in double the pace in the paint shop due to the easier to use interface we designed. This proved the amount of value add a seamless UI can have on a business process.